Concrete leveling
In civil engineering, concrete leveling is a procedure that attempts to correct an uneven concrete surface by altering the foundation that the surface sits upon. It is a cheaper alternative to having replacement concrete poured, and is commonly performed at small businesses and private homes as well as at factories, warehouses, airports and on roads, highways and other infrastructure.
Causes of Concrete Settlement
Concrete slabs can be susceptible to settlement from a wide variety of factors. In some areas of the United States, naturally occurring soils can consolidate over time, including areas ranging from Texas up through to Wisconsin. Soil erosion also contributes to concrete settlement, which is very common for locations with improper drainage. Concrete slabs built upon filled-in land can excessively settle as well. This is common for homes with basement levels since the fill on the outside of the foundation frequently is not compacted properly. In some cases, sidewalk or patio slabs pitch down, directing water down towards the basement level. Tree roots can actually heave a slab upwards; this is quite common along public roadways, especially within metropolitan areas.
Concrete settlement, uneven concrete surfaces, and uneven footings can also be caused by seismic activity especially in earthquake-prone countries including Japan, New Zealand, Turkey and United States.
What is Slabjacking
Slabjacking is a specialty concrete repair technology. In essence, slabjacking attempts to lift a sunken concrete slab by pumping a grout through the concrete, effectively pushing it up from below. The process is also commonly referred to as "mudjacking" and "pressure grouting" as well.
Accounts of raising large concrete slabs through the use of hydraulic pressure date back to the early 1900s. Early contractors used a mixture of locally available soils (sometimes including crushed limestone and/or cement for strength), producing a "mud-like" substance and thus the term "mudjacking." Modern slabjacking contractors can now use an expanding polyurethane foam, providing a multitude of benefits when compared to traditional slabjacking materials.
The slabjacking process generally starts with drilling small diameter access holes in the concrete, strategically located to maximize lift. These holes are generally 3/8" or 5/8" diameter for urethane slabjacking and can be over 2" in diameter for traditional mudjacking applications.
Initial material injections will fill any underslab void space. Once the void space is filled, subsequent injections will start lifting the concrete within minutes. After the slabs are lifted, the access holes are patched and the work is complete.
The process is very rapid when compared to traditional "rip and replace" applications and is minimally disturbing to the surrounding areas.
Slabjacking technology has several limitations. Most importantly, poor quality concrete may crack and/or deteriorate when being lifted. This is especially true for slabs that are less than 4 inches in thickness. Cracks can also develop in the concrete during the lifting process. Slabs built over filled-in land and/or poor subsoils can also be susceptible to further settlement.
Expanding Structural Foam leveling
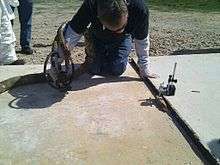
Foam leveling uses closed cell polymer expanding foam in an injection process.[1] A two part polymer (example, components A and B [2] is injected through a hole less than one inch in diameter, typically 5/8." Although the material is injected at a higher psi rate than traditional cementitious grouts, the pressure is not what causes the lifting. The expansion of the air bubbles in the injected material below the slab surface performs the actual lifting action as the liquid resin reacts and becomes a structural foam. Material injected below a slab to be lifted will first find weak soils, expanding into them in such a manner as to consolidate and cause sub-soils to become more dense and fill any voids below the slab. One inherent property of expanding foams is that they will follow the path of least resistance, expanding in all directions. Another inherent property includes reaching a hydro-insensitive or hydrophobic state when cured with 100% cure times as little as 30 minutes. Closed cell polymer foams offer benefits that go beyond the goal of leveling hard surfaces. They will not retain moisture, which in northern climates can cause frost heaving. They are not subject to erosion once in place. Their fast cure time allows for immediate use when application is complete. Their light weight, 3 to 8 lbs. per cubic ft. vs. 100 to 120 lbs. per cubic ft. for cementitious grout will not cause further settlement. Foams will retain their cured shape and volume indefinitely reducing the possibility of new voids forming below grade to nearly zero unless acted upon by some outside cause. Some closed cell polymer foams have baseline lifting capabilities of 6,000 lbs per sq. ft. and leveling procedures have been performed in which loads as high as 125 tons have been lifted and stabilized in a surface area of less than 900 sq. ft.
Some foams are even stronger, with compressive strengths of 50 psi and 100 psi in a free rise state. That’s equal to 7,200 to 14,000 lbs per square ft of support. [3]
References
- ↑ Sivertsen, Katrine (Spring 2007). "Polymer Foams, 3.063 Polymer Physics" (PDF). Retrieved 14 Feb 2013.
- ↑ "Technical Data Sheet, Precision Lift 4.0# - Components A and B" (PDF). Prime Resins, Inc. 2015-03-31. Retrieved 13 April 2016.
- ↑ "Slab Jacking With Polyurethane Foam – How Strong is Strong Enough?". Alchemy Polymers. 2013-06-12. Retrieved 9 September 2016.