Fiber cement siding

Fiber cement siding (or "fibre cement cladding" in the UK and Australasia) is a building material used to cover the exterior of a building in both commercial and domestic applications. Fiber cement is a composite material made of sand, cement and cellulose fibers.
Usage
In appearance fiber cement siding most often consists of overlapping horizontal boards, imitating wooden siding, clapboard and imitation shingles. Fiber cement siding is also manufactured in a sheet form and is used not only as cladding but is also commonly used as a soffit / eave lining and as a tile underlay on decks and in bathrooms. Fiber cement siding is not only used as an exterior siding, it can also be utilized as a substitute for timber fascias and bargeboards in high fire areas.
Specifications
Sheet sizes vary slightly from manufacturer to manufacturer but generally they range between 2400 – 3000 mm in length and 900 –1200mm in width (600 & 450 mm increments). This manufactured size minimizes on-site wastage as residential floor, wall and roof structures lay structural members at 450 or 600 centres.
When used as siding boards, widths between 130mm and 300mm (5.25 inch to 12 inch) are available.[1]
Fiber cement thicknesses vary between 4.5-18mm and also vary in density – the lower density resulting in a fibrous rough edge when cut and the higher density having a cleaner smoother edge when cut.
Thermal resistance and sound transmission vary greatly between fiber cement products. Fiber cement sheet products rate poorly in thermal resistance and sound transmission and separate wall insulation is highly recommended. Generally the thicker and denser the product the better resistance it will have to temperature and sound transmission.
Installation
Fiber cement cladding is a very heavy product and requires two people to carry the uncut sheets. Thin fiber cement cladding is fragile before installation and must be handled carefully; it is prone to chipping and breakage if improperly handled.
Once the product is cut it may again require two people to install – one to hold the sheet flush against studwork and the other to nail the product in place.
Cutting fiber cement cladding sheeting usually requires a mechanised saw or metal hand shears and sheets can be cut to size in three ways:
- Thinner sheets can be scored with a heavy duty cutting blade and snapped
- Purpose made "fibro cutter" (an Australian term)
- Thicker and denser sheets require cutting by a mechanical saw using a diamond blade (Masonry blade)
- 1/8 spacing required between end-joints (cladding seams) later to be filled with caulking made for fiber cement siding
- Metal 6"x6" step flashing required behind overlapping seams to prevent sheathing damage from water
- Hot dipped Galvanized roofing nails to hang fiber cement siding
Some caution must be exercised to properly ventilate areas where fiber cement siding (FCS) is being cut; long-term exposure to the silica dust generated during the installation process can cause silicosis.
Fiber cement cladding can be painted before or after installation. (For areas of exposure, weatherproof paint must be used.) Once the product is fixed the joints are usually covered with timber battens and the entire wall surface is painted.

History
Ludwig Hatschek patented fiber cement in Austria in 1901 and named it "Eternit" based on the Latin term "aeternitas" meaning everlasting. In 1903 the company Schweizerische Eternit-Werke AG began fabricating the material in the city of Niederurnen in Switzerland. Early fiber cement panels used asbestos fibers to add strength. Fiber cement products came about as a replacement for the widely used "asbestos cement sheeting" or "fibro", manufactured until the 1980s.
Durability
The external cladding products require very little maintenance once installed and painted. The thicker/denser fiber cement products have excellent impact resistance but the thinner less dense products need to be protected from impact. Compared to wooden siding, fiber cement is not susceptible to termites or rot.[2]
Fiber cement siding using base board materials that have been classified, by accredited laboratories, as Category A according to BS EN 12467: 2004 Fiber-cement flat sheets - Product specification and test methods are sidings which are intended for applications where they may be subject to heat, high moisture and severe frost.
Fire resistance
Fiber cement cladding is a non combustible material which is widely used in high bush fire prone areas throughout Australia . Pictured above is James Hardie's Fiber Cement cladding ‘Scyon Linea’ weatherboard which has been substituted for the traditional timber fascia and barge board materials.
While the best possible Reaction to Fire Classifications are A1 (construction applications) and A1Fl (flooring applications) respectively, both of which mean "non-combustible" according to European standard EN 13501-1: 2007, as classified by a notified laboratory in Europe, some fiber cement boards only come with Fire Classification of A2 (limited combustibility) or even lower classifications, if they are tested at all.
Safety
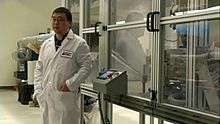
As mentioned previously, long-term exposure to silica dust generated by cutting fiber cement siding during installation can lead to silicosis and other lung diseases among workers.[3] Researchers at the National Institute for Occupational Safety and Health (NIOSH) confirmed these findings, showing that many of the silica dust particles are in the respirable fraction, able to penetrate the deepest parts of the lung.[4] Laboratory tests performed by cutting fiber cement siding within an isolated chamber showed that by connecting a regular shop vacuum to a circular saw, exposures to silica dust produced by the cutting can be reduced by 80-90%.[5] Later, NIOSH completed four field surveys where construction workers cut fiber cement siding. Results showed that exposure to silica dust was controlled below the NIOSH Recommended Exposure Limit (REL) for respirable crystalline silica (0.05 mg/m3) when a regular shop vacuum was used.[6]
Alternatives
Competitors to fiber cement cladding include products made from vinyl, polyvinyl chloride, wood composite products (such as hardboard and Masonite) and aluminum siding
See also
References
- ↑ "HardiePlank Lap Siding" (PDF). Oct 2012. p. 84.
- ↑ Ball, John E. "Mineral-Fiber Siding". Light construction techniques: from foundation to finish. Reston, VA: Reston. p. 189. ISBN 0-8359-4035-7.
- ↑ Fairfax, R; Lofgren, DJ; Johnson, DC; Walley, TL (2004). "OSHA Compliance Issues". JOEH. 1 (1): D1–D6. doi:10.1080/15459620490264418.
- ↑ Qi, Chaolong (March 26, 2013). "CDC - NIOSH Science Blog - Contractors Wanted: Help NIOSH Advance Research to Protect Workers from Silica". Centers for Disease Control and Prevention. Retrieved June 6, 2013.
- ↑ Garrett Burnett (director), Chaolong Qi (2013). Cutting fiber cement siding - silica dust and lung disease - YouTube (YouTube Video). Cincinnati, OH: National Institute for Occupational Safety and Health.
- ↑ NIOSH [2015]. Reducing hazardous dust exposure when cutting fiber-cement siding. By Qi C, Whalen JJ. Cincinnati, OH: U.S. Department of Health and Human Services, Centers for Disease Control and Prevention, National Institute for Occupational Safety and Health. DHHS (NIOSH) Publication No. 2015-185.